DX of Materials Development: A Chemical Manufacturer Tackling the Challenge of Materials Informatics
Jan. 9, 2024
Xin Luo
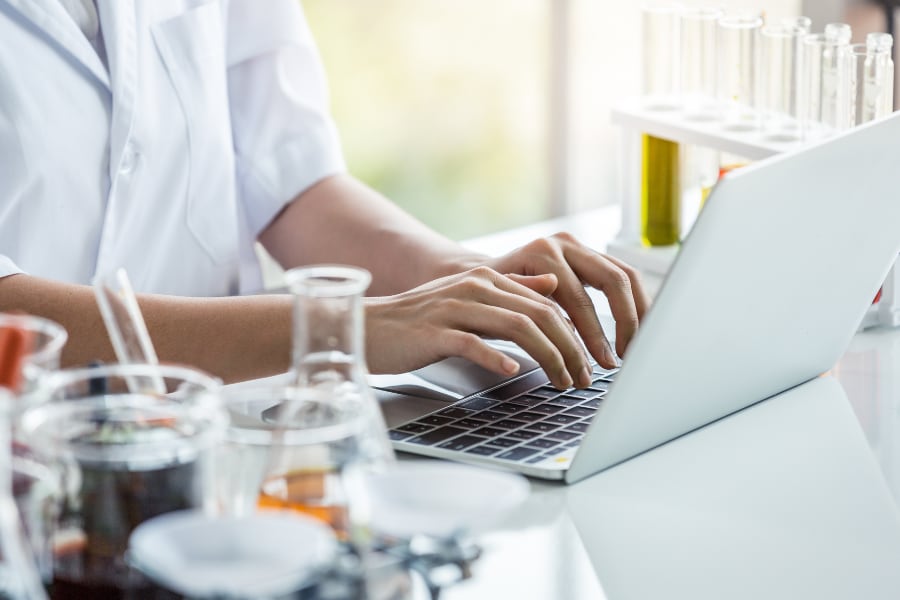
Materials with new performance and usefulness for our daily lives have been created through decades of repeated experiments and evaluations. However, digital transformation (DX) through information science is radically changing this traditional method, named as “Materials Informatics” (MI). This article will introduce the true nature and outlook of DX in materials development based on a case study that is happening right now at SEKISUI CHEMICAL, a chemical manufacturer.
Tight deadlines
“In the past, materials development took up to 10 years to complete in some cases, but these days, results are expected in six months or no longer than one to two years,” says Mr. Yoshikazu Masuyama, who works at the Materials Informatics Group at SEKISUI CHEMICAL's Innovative Informational Intelligence Center. He explained the sense of urgency on the frontlines of materials development.
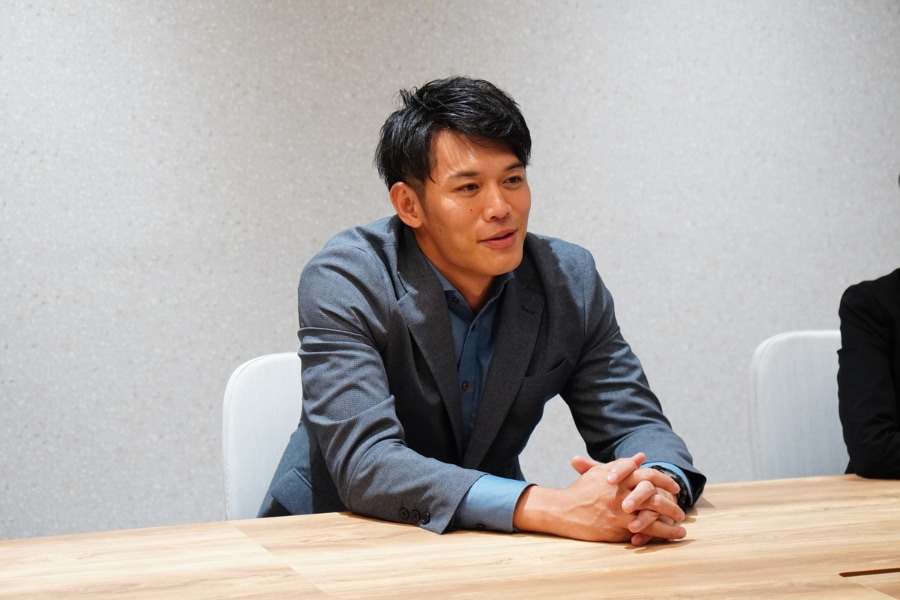
SEKISUI CHEMICAL is a chemical manufacturer that was founded in 1947, and it produces materials used in houses and factories, such as pipes and rain gutters, along with materials used in cars and electronic equipment, such as tapes, films, and foams. The company has been developing new materials to meet the needs of the times, but the shortening of product life cycles has dramatically changed the development environment.
For example, new models of computers, tablets, and other electronic devices are now released every year with major model changes. The features that act as the centerpieces of these products are constantly increasing, and consumers are replacing them in a short period of time in pursuit of new features. As the time that can be spent on product development decreases, SEKISUI CHEMICAL is receiving requests in rapid succession to develop materials with new performance.
Additionally, the performance of the required materials is becoming more diverse. From the standpoint of environmental considerations, they expect to receive requests for materials that simultaneously require conflicting performance capabilities; that is, they should be both durable and easily recyclable. Delivery times are becoming shorter, but products that are difficult to develop are increasing.
Increasing the speed of materials design by 900 times
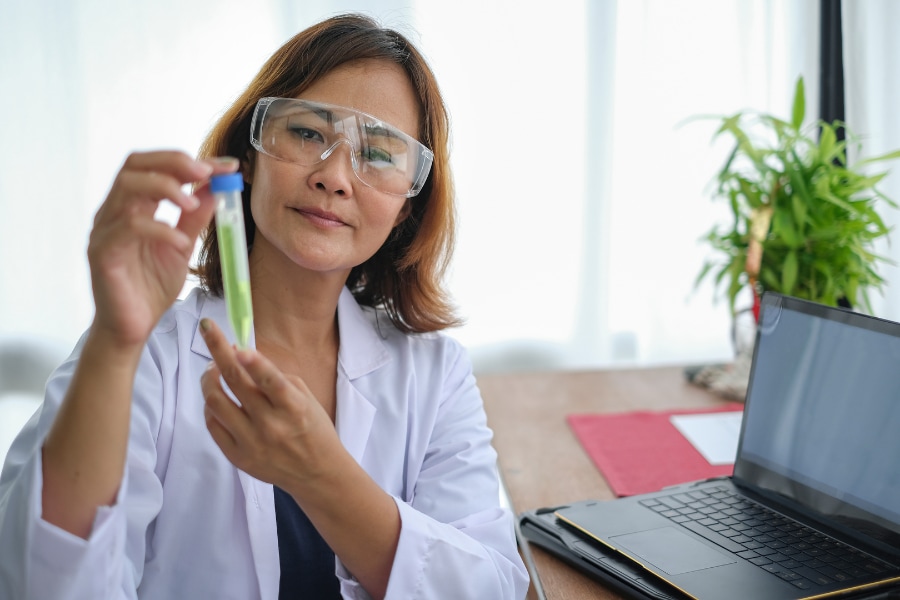
To overcome this situation, SEKISUI CHEMICAL attempted to utilize MI. The development of materials is carried out in stages: “goal setting,” “technical research,” “materials design,” “planning of experiments,” and “experiments and evaluations.” In order to reduce development time, they first focused on “materials design.”
In the past, materials design involved researchers devising combinations of materials and synthesis procedures based on their own experience. The number of combinations is enormous, in the order of hundreds of thousands, and it takes a long period of time to narrow down the optimal combination.
In an effort to shorten this period, SEKISUI CHEMICAL gathered together past experimental methods and results which researchers had independently owned and converted them into data. This data is then used for predictions using AI. Instead of researchers, AI predicts results from the data of experimental methods, such as formulations and synthesis procedures, and finds the optimal combination. As a result, the time required for material design in the development of film, which previously took five months, was reduced to four hours, which is approximately 900 times faster.
To realize the inherent innovation required of researchers
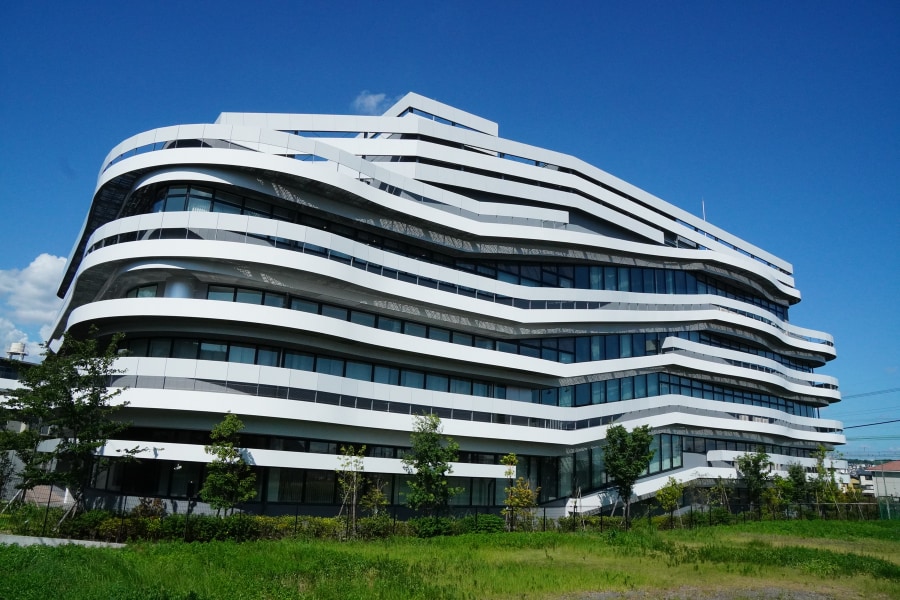
Mr. Masuyama, who is also a researcher himself, cites two advantages of MI.
“The first is that researchers can devote themselves to development. Less time is spent on simple tasks, allowing researchers to focus on innovation.”
MI allows researchers to focus more on the material itself. Up until now, they have been pressed for time and have only been able to look at the results of their experiments numerically, but when they have more time, they are able to fully think about the materials, and he says: “I am sure that researchers will be able to realize their true potential and make new discoveries.”
“The second advantage is that synergy can be achieved by taking past results without omission and multiplying them. Individual researchers alone can only tackle development within their own limited scope and based on their own experience. This inevitably means a ceiling will be reached and will have adverse effects.”
In fact, there was a case in which a researcher was planning to conduct an experiment after designing a material but where another researcher had already completed the same experiment and left the results in-house. Moreover, when development is based on personal experience, there is a tendency to be reluctant to deviate from methods that the researcher has used in the past. MI has the appeal of transcending the limits of individual experience and knowledge—in other words, the limits of the individual.
The difficulty of collecting data
Having succeeded in reducing the time required for materials design, SEKISUI CHEMICAL saw the potential for innovation and attempted to expand MI. However, they ran into a roadblock: the difficulty of collecting data. Even a single researcher has hundreds of individual experiment records. The amount of data to be collected from all researchers at the company would be enormous. The challenge was to create a comprehensive, centralized database of such data. It was also difficult to collect all the information obtained in the experimental process.
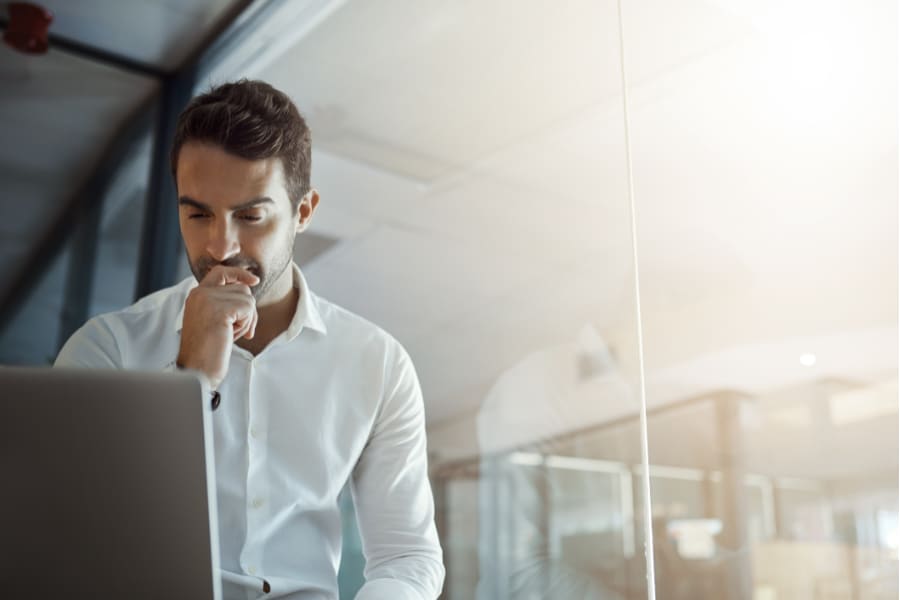
Mr. Masuyama said: “If we only ask for uniform data input, information will be overlooked. For example, notes made on a whim during an experiment would be omitted.”
Therefore, SEKISUI CHEMICAL decided to collaborate with Hitachi, which had been supporting MI for manufacturers using the latest digital solutions, and first began organizing various in-house data using Hitachi's proprietary digital technology and AI in order to create a database. Additionally, SEKISUI CHEMICAL has also begun to utilize information on materials development published by the government and other research institutes in combination with their database.
This will reduce the time required for technical research and increase the possibility of developing materials with new performance by designing materials using a wide range of data.
Experiments and data collection to be automated in collaboration with Hitachi
SEKISUI CHEMICAL and Hitachi are also collaborating to promote MI in experiments and evaluations with the goal of enabling experiments and evaluations in a virtual space in the same manner as in the real world by utilizing digital twin technology, which accurately reproduces the experimental environment in a virtual space based on data collected from instruments and devices in the real world.
If this can be achieved, it will enable experiments and evaluations to be performed anywhere using computers. Furthermore, in the world of the digital twin, where everything is composed of data, there is the possibility of acquiring data that could not be obtained from physical devices until now.
Automating experiments will also free up more time for innovation. It is hoped that MI will streamline the various stages of materials development and that it will lead to the discovery of more materials with new performance potential.
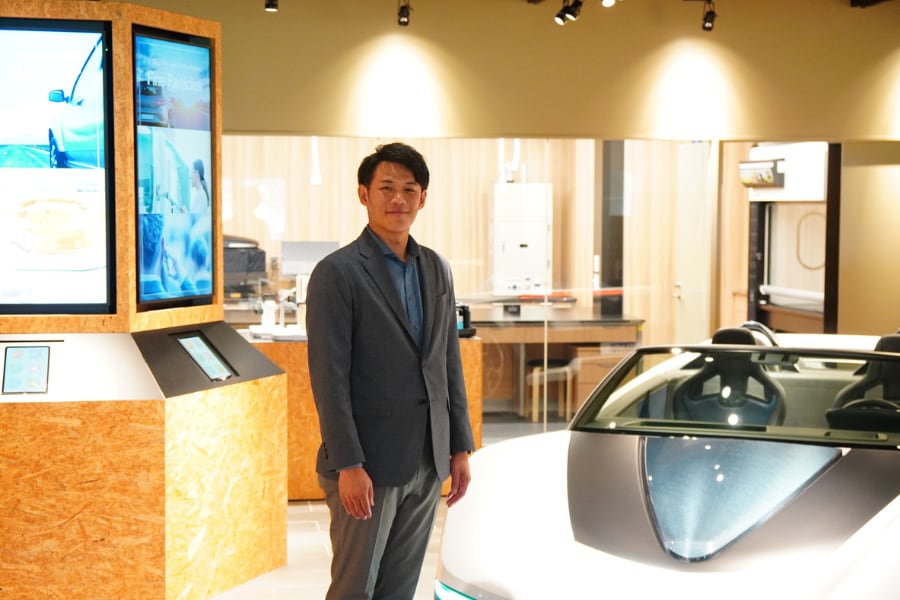
Mr. Masuyama emphasizes that, rather than being an extension of the past, materials development, which has been a repetitive process of design, experiment, and evaluation, must change.
“Society is made up of a small world of materials. All things are made of materials. Society will not change without first bringing about innovation in that small world. That is why MI is necessary.”
Toward the better society, Hitachi will continue to support innovation in materials development through MI that makes full use of data and digital solutions.