Recycled Plastic for DX: New Storage for Data Centers
Jan. 17, 2024
Xin Luo
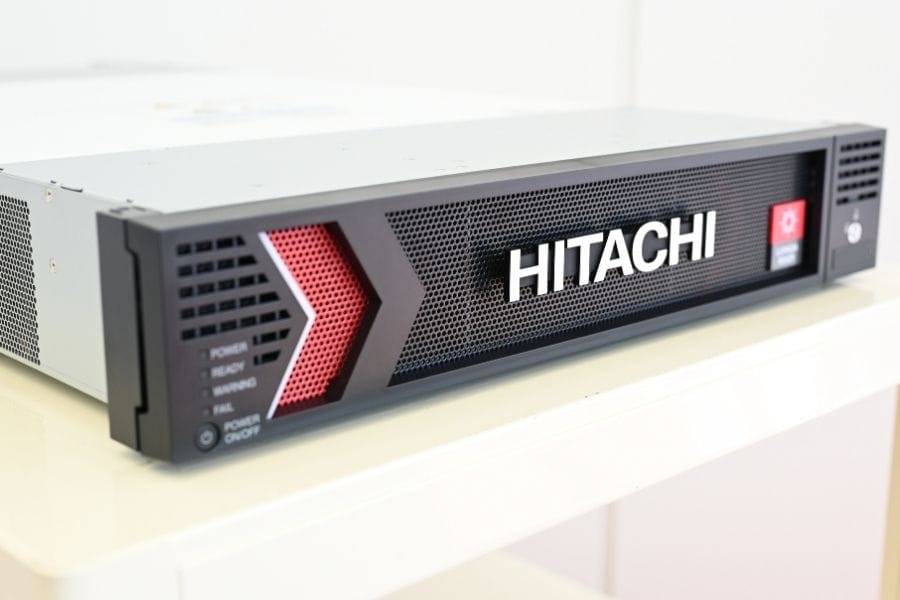
More and more data centers have been built in recent years in accordance with the acceleration of data-driven digital transformation (DX). Computers and related electronic equipment, such as servers, network equipment, and storage systems, are housed at data centers. The emergence of the latest AI, such as generative AI, which learns from large language models (LLMs), has increased the demand for storage systems to store large amounts of data. Although the data to be stored is digital, the storage system exists in a physical form, and the components that make up the storage system contain plastic. This article looks at an attempt to realize a data-driven society while reducing the consumption of plastic, which can cause environmental problems.
What are storage systems?
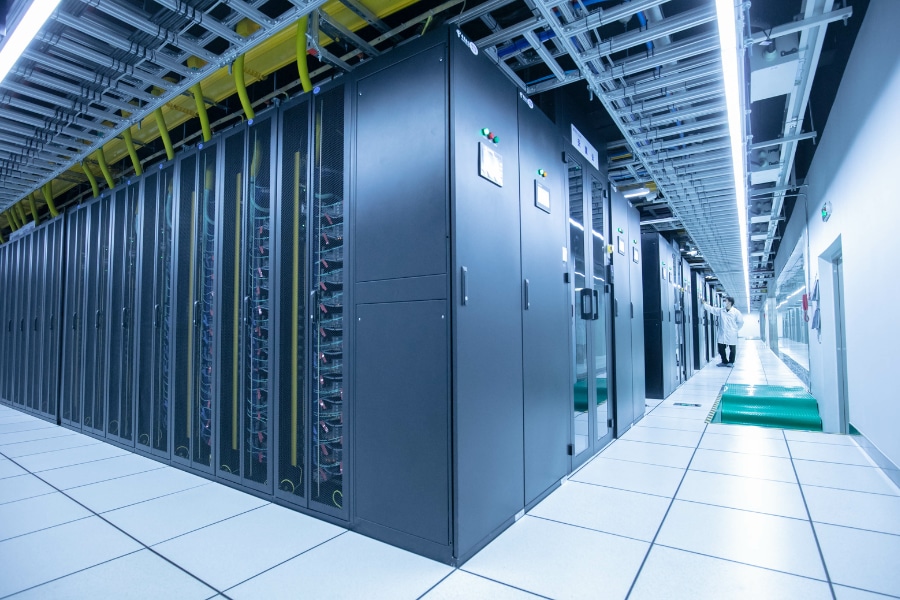
Storage systems, synonymous with storage media, are used to store data, and the ability to save photos and videos and download applications onto computers and smartphones is possible because of storage systems built into those devices.
Companies also store various types of data in data center storage systems to provide services and for production activities. As companies handle large amounts of data, they need a lot of storage space, too.
The amount of data that needs to be stored has been increasing in recent times due to the promotion of DX and the advent of AI, in which calculations are required that use a large amount of data. Additionally, the way that individuals store data is changing due to data shared in the cloud via the internet. Storage in the cloud is provided by companies setting up storage systems in data centers.
Saving power and reducing plastic waste
Storage systems are electronic and therefore consume electricity when storing and calling data. We rely on thermal power plants which emits CO2. Therefore, efforts are underway to improve storage system performance to save power.
Apart from power saving, there is another aspect that must be taken into consideration for the environment: Storage systems that store digital data are devices that physically exist in the world, and they are made of metal and plastic.
Plastic is durable and can be easily formed into various shapes, and while it is convenient, it can also cause problems in the natural environment after it is used. Storage systems are replaced with new ones every about five to seven years, and the degraded plastic used as parts then becomes waste.
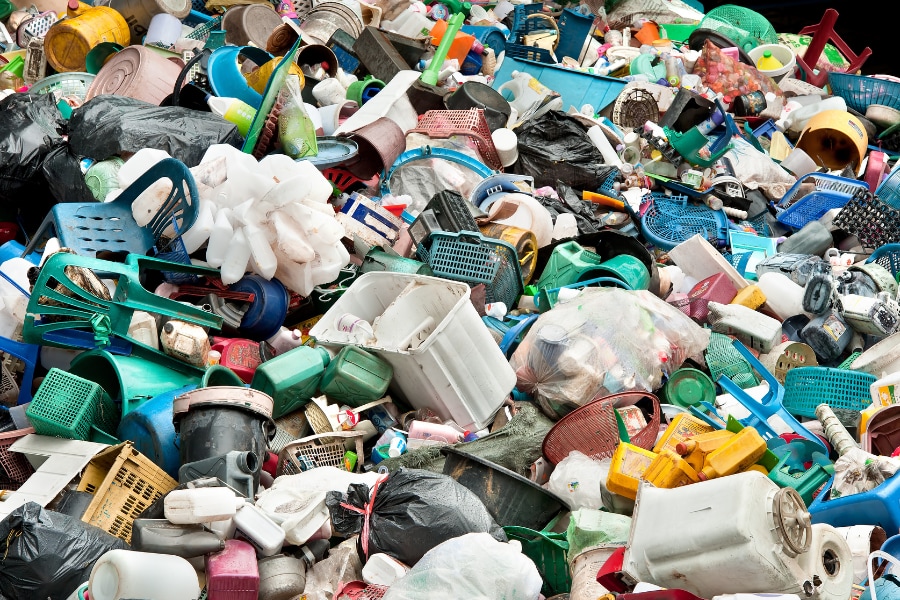
Plastic does not decompose easily, due to its superior durability, making it difficult to return it to nature, and it has the potential to alter the natural environment in unexpected ways. Additionally, plastic is mainly made from crude oil, a fossil fuel, which emits large amounts of CO2 when burned.
Challenge of using recycled materials
“From around 2020, our customers started asking us if we could use recycled materials for the plastic used in data center storage systems,” said Kenichi Miyamoto, a storage system designer at Hitachi, Ltd.
Since that time, recycled materials have been used in electronic devices for personal use, such as laptop computers and monitors. However, there was a barrier that had to be overcome to use recycled materials in data center storage systems.
Data center storage systems consume many times more power and are used non-stop for many hours compared to electronic equipment used at home. “The power consumption of a single storage system is akin to using several microwave ovens continuously," says Miyamoto.
Therefore, the materials used need to comply with high safety standards, as high power consumption makes them more susceptible to heat. Materials are required that are not flammable and that ensure that fire does not spread even if they were to catch fire. However, recycled plastics for such applications had not yet been developed.
Moreover, recycled plastic made from recycled raw materials consist of a mixture of plastics that were used for various purposes. As the plastic has aged in the original product before it was recycled and is then repeatedly heated to process it into recycled raw materials, the plastic quality is inevitably variable and prone to deterioration.
Reducing CO2 emissions by 40%
Stumped, Hitachi consulted with Teijin, a chemicals manufacturer with whom it had been collaborating in materials development. Mr. Masahiro Kozu of Teijin recalls: “It was difficult to find a recycled plastic that would immediately comply with their very high requirements.”
This was because, in plastic manufacturing, there is a trade-off, as increasing flame resistance makes the plastic prone to degradation and decreases strength. If recycled raw materials are used, they are even more susceptible to degradation and reduction in strength. Teijin therefore embarked on developing a new product, firstly turning its attention to Multilon,which is a plastic that combines polycarbonate and acrylonitrile butadiene styrene (ABS) resin.
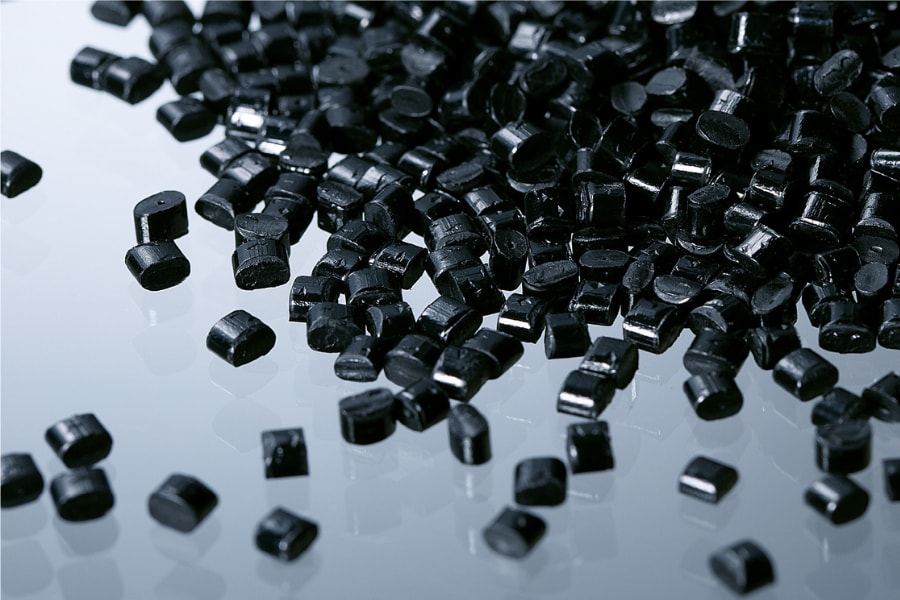
Originally, Hitachi storage systems used a plastic that was a combination of polycarbonate and ABS resin, and they judged that it would be easily adoptable. However, while there were various grades (types) of Multilon available, including some that were made from recycled materials, they did not comply with the required safety standards.
Therefore, Teijin repeated simulations and experiments with its own know-how and, after about a year, found a suitable blending method for recycled raw materials. The source materials were disused plastics, such as CD and DVD disks, water bottles for water servers, and automotive headlight covers. The new grade, which is 40% recycled material by weight, is both highly flame resistant and strong.
Mr. Kozu confidently said: “At our company, this grade has the highest percentage of recycled materials while meeting the high safety standards required for storage systems. Teijin estimates that the new grade reduces CO2 emissions by as much as 40% compared to conventional plastics produced and shipped without recycled materials, that is, from drilling oil."
Goal: Using more than 50% of recycled materials
Hitachi's new storage system uses this recycled plastic for the bezel, which is the cover on the front of the storage system. The bezel serves to protect the contents of the storage system, and the very conditions for its use were flame resistance and strength.
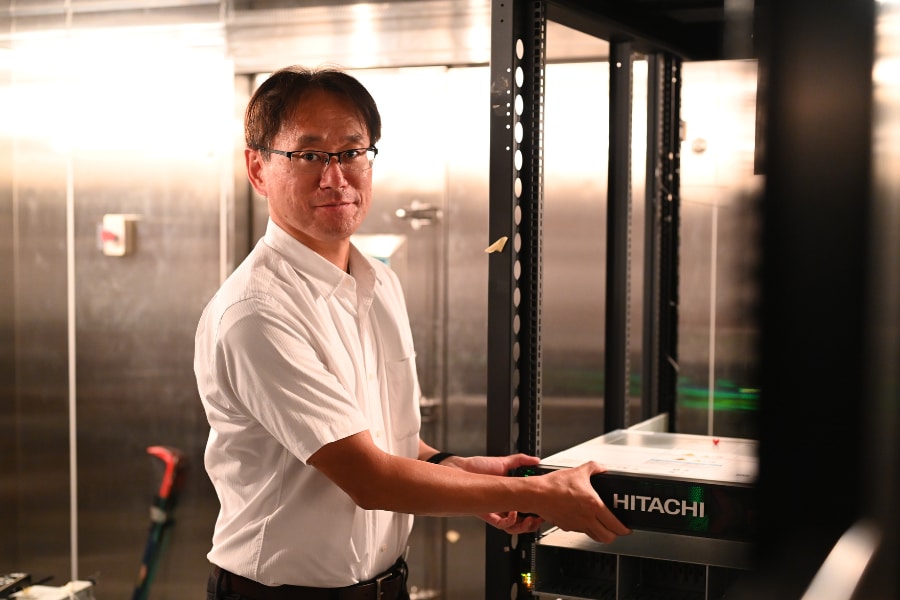
Only about 5% of the storage system's replaceable plastic could be made from recycled materials. “Using recycled plastic in data center storage systems is a new trial and an important first step to increase the use of recycled plastic. We will continue to expand our efforts for the sake of the global environment," remarked Miyamoto, enthusiastically.
In the future, Hitachi plans to expand the use of recycled plastic to the canister that holds the disk drives used for data storage systems with the goal to use more than 50% recycled materials by FY2030. Hitachi is also considering the use of biomass materials, such as plant-derived materials, and the recovery of plastics used in storage systems that are no longer serving their role.
“When things are no longer used, they are destined to be thrown away. However, if we can eliminate waste and recirculate it, we can benefit both people's lives and the natural environment," says Miyamoto, with high expectations. Innovations that support our daily lives are advancing in a variety of fields.