Supermarket Improves Operational Efficiency via an Automatic Ordering System Based on Demand Forecasting
Mar. 27, 2023
Hiroki Ikarashi
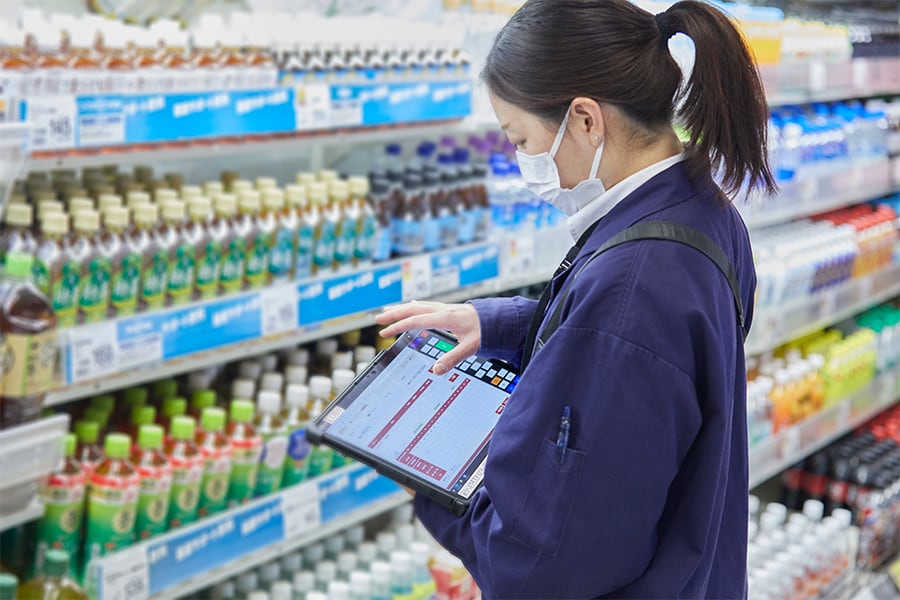
In Japan, amid a backdrop of a decline in the working population due to falling birthrates and an aging society, supermarkets are taking advantage of digital technology to accelerate labor saving. YAOKO CO., LTD., which operates 182 supermarkets in the Kanto region, is one such company. It has dramatically increased operational efficiency by automating the ordering work previously performed manually by skilled personnel.
The company deployed an automated ordering system developed by Hitachi, Ltd. that forecasts merchandise demand and that automatically allocates the appropriate order quantities based on that demand, and there are high expectations that this will accelerate digital transformation (DX) in the retail industry. This is an interview with representatives from both YAOKO and Hitachi to learn more about the system.
Forecasting demand and automatically ordering merchandise

The automated ordering system is linked to a shelf allocation system that determines merchandise displays and a core system that manages inventory, and it also incorporates data related to day of week, season, surrounding environment, and other factors so as to make sophisticated demand forecasts. Based on these forecasts, the system suggests the appropriate order quantities, which are then adjusted as necessary by store personnel before the order is placed.
Once the merchandises are put on the shelves, sales data on the actual number of merchandises sold is stored in a database for all stores and is fed back for the next demand forecast. In this way, accuracy is improved by repeating forecasts and suggestions while accumulating data that is updated daily.
The automated ordering system is based on Hitachi's "Hitachi Digital Solution for Retail/Automatic Ordering Service Based on Demand Forecasting " which has a proven track record at supermarkets and major retailers and which uses Optimum Architect's cutting-edge technology, Category Profit Management (CPM).
Digitally transforming labor-intensive ordering work

YAOKO CO., LTD., which operates supermarkets mainly in the Kanto region, deployed this system in November 2022.
Previously, orders had been placed manually by skilled personnel, but this had the problem of making the work dependent on specific employees. To solve these problems, YAOKO previously rolled out an automated ordering system made by another company. Mr. Takayuki Nakajima, YAOKO's division chief of the processed foods section, says that, in addition to eliminating the need to rely on certain personnel, he also wanted to improve operational efficiency and increase profits by eliminating wasteful ordering.
“Orders were being placed manually by certain employees, so we decided to automate and optimize the ordering process to address possible labor shortages in the future," he said.
However, the automated ordering system that was rolled out was a "sell-one-by-one" system that ordered only what was sold and in the quantity sold, so it did not respond to fluctuations in demand, and shortages were found to be detrimental to shoppers' convenience. Furthermore, the ordering accuracy did not meet YAOKO’s expectations.
Therefore, YAOKO held a competition for companies to pitch their ordering systems, which Hitachi won because of developing a system that proposes a “demand forecasting ordering” system as an automated ordering system that forecasts demand and because it had a track record of being used by other companies.
Development began in December 2020, just as COVID-19 was beginning to spread again. Yoshimasa Otogawa of Hitachi, who was in charge of development, recalls that time.
“A state of emergency was declared immediately after our first face-to-face meeting, so team meetings were basically held remotely from that point. The first challenge was how to enable the team members to communicate with each other given the physical restrictions.”
The challenge of “tuning”
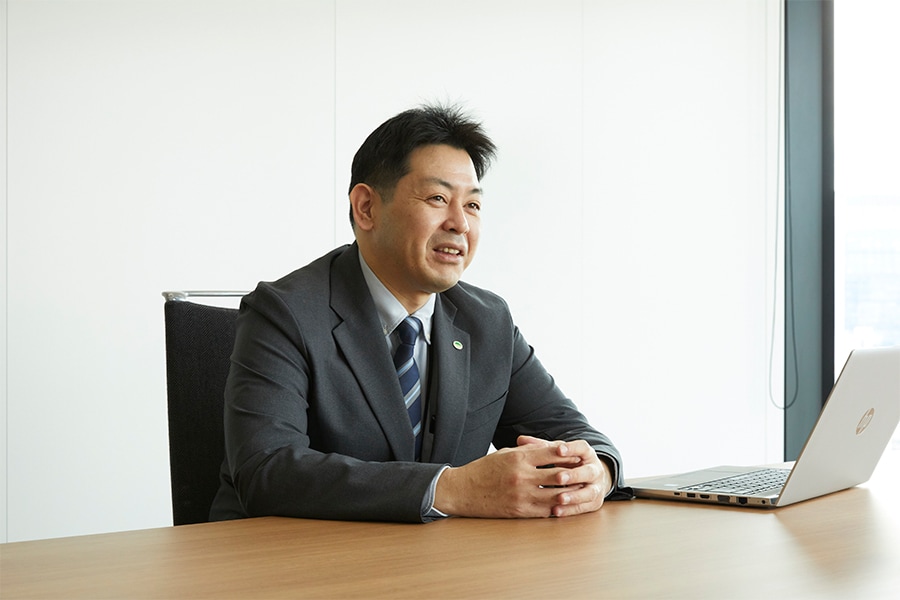
The development of the automated ordering system began in this way, but the team faced a number of challenges. One of them was the fine tuning of the system.
Supermarkets reference a wide variety of factors to determine the amount of merchandise to order. For example, day of week, season, amount of inventory, amount of waste, surrounding environment, and events, such as special sales and discounts, must all be considered.
In particular, "daily delivery" foods, such as bread and milk, are subject to a combination of use-by dates, and "we had to repeatedly perform tuning that made our heads’ spin," remarked Otogawa.
What made tuning even more difficult was the set of circumstances unique to YAOKO's stores. Mr. Nakajima of YAOKO, who led the development project, said the following:
“Our 182 stores each have their own unique characteristics. The sales floor space ranges from about 1,150 m2 to 3,000 m2, and sales vary five-fold from store to store. Location varies, too: some stores are located in front of train stations, and sales are at their peak in the evening, while others are in residential areas and sell large quantities on weekends. Each store is truly unique. So at first, we were unsure if this system would really fit our unique situation.”
Proof-of-concept testing began at two stores in June 2021. The results were reflected in improvements to enhance the accuracy of the system. Meetings were held weekly, and a new version was released every time modifications were made. This is what is called "agile development," whereby effectiveness is measured and feedback is provided immediately. The process took about two and a half years.
“It was a cycle of ‘three steps forward, two steps back’. There were many times when the tuned version was different from what we had expected, but I think it was significant that we worked as one team with the relevant departments within our company and with Hitachi to fill in the gaps.” said Mr.Nakajima.
Achieving improved productivity and reduced food loss
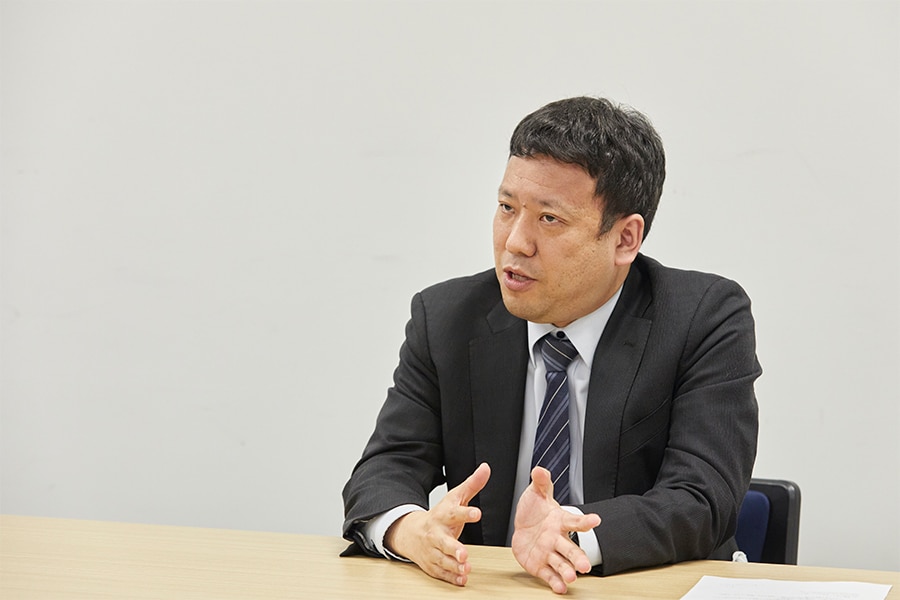
After overcoming these difficulties, the automated ordering system was finally completed. The "automation rate" (the ratio of automatic ordering system proposals that are adopted as-is) at the stores where the system was deployed has improved dramatically at the Grocery Department, which handles general foods and sundries, from 65% with the previous system to 98% now.
Furthermore, the time required to place an order at the stores where proof-of-concept testing was conducted was reduced from 3 hours to 25 minutes, which is an 85% reduction. Significant reductions were also recorded at all stores. This has made it possible to greatly automate the work of the person in charge of ordering, freeing up time for other tasks, such as customer service and picking merchandises for the online supermarket.
Mr. Nakajima of YAOKO said: “Previously, sales varied from store to store, but the automation of ordering across all stores has enabled us to efficiently procure an assortment of merchandises on average, which has led to an improvement in our sales capabilities. Moreover, if there is no difference in results irrespective of who is in charge, and if the automated ordering can be trusted to automatically order goods, staff should be able to take time off with peace of mind. We expect that this will lead to a change in the way we work."
Furthermore, by eliminating wasteful ordering, the number of food products that are disposed of has been reduced. Depending on the month, a reduction of 5 to 15% can be accomplished, which is expected to contribute to the elimination of food loss.
In talking about prospects for the automated ordering system, Hitachi's Otogawa said that he hopes to increase its performance by involving not only retailers but also manufacturers and the field of logistics.
“Hitachi's demand forecasting has proven itself in the logistics and wholesale industries, and we think that in the future we will be able to share information with manufacturers as well. By doing so, we hope to improve productivity throughout the supply chain by linking data and eliminating waste.”
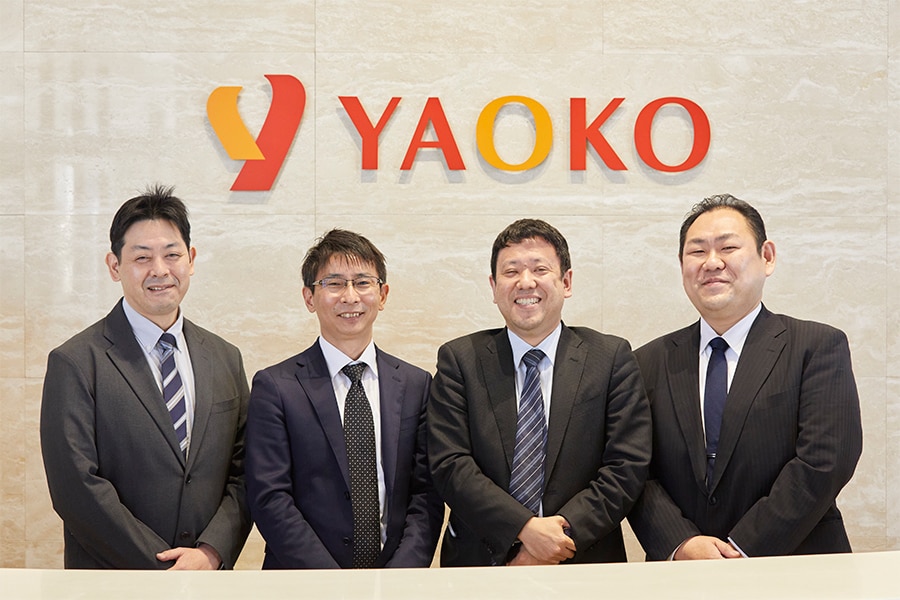